

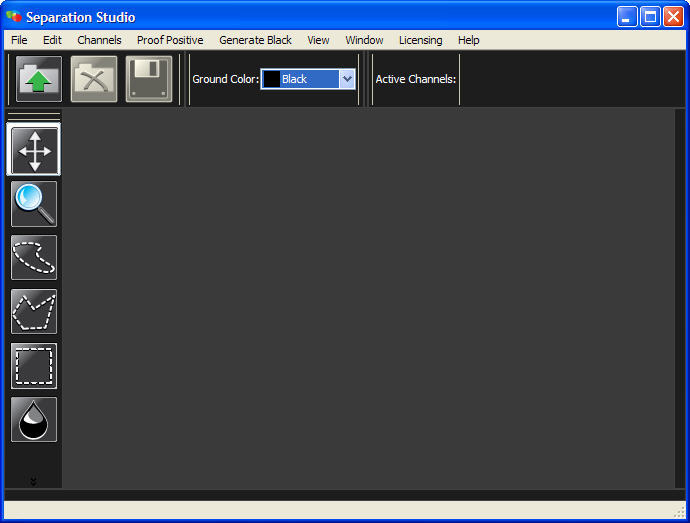
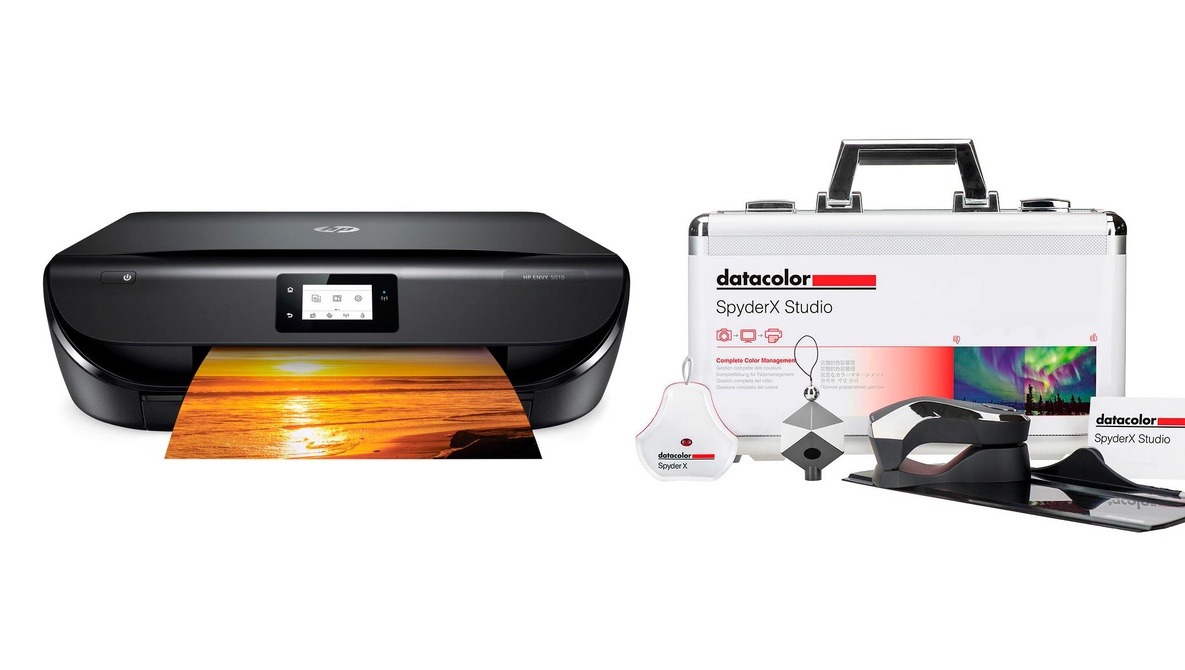
Alternatively, you can establish which sections of the vat aren’t affected and print only in those areas. You can either replace the interface layer or purchase a new vat. To fix this problem you have two choices. Take note that if you ignore this problem you will end up with a partially useless build plate because certain sections become unviable. In either case, after several prints, you’ll encounter issues with the interface layer due to wear and tear. The cheaper bottom-up printers use the same concept by pushing a thin layer of resin at the start of the printing process. Inspect the interface layer: Nowadays, most resin printers have a thin interface layer at the bottom of the vat.
#Separation studio printing problems how to
To fix this issue, you’ll have to examine your printer’s instructions or look for specific tutorials on how to calibrate the print bed or vat. Another clue is a flat piece of resin hardening on the interface layer once you finish printing. So, if you notice a particular section of the print adhering to the plate then maybe that section isn’t correctly set inside the vat. This is a common step that has to be taken when working with common FDM printers as well. Level the bed or vat: If your printer doesn’t come with an automatic leveling system, you’ll have to manually level the vat.This is especially important if you’re printing tall models. In this case, you should reposition the print where the peeling force is at its minimum. Check the print’s position: If your resin printer has a tilting vat to help prevent peeling, there will be sections of the plate that are exposed to higher stress.Sometimes we only need a marginal difference and warming up the room temperature does the trick. So check the temperature of the resin and heat it if necessary. Check the temperature: In a lot of cases, the temperature is simply too low for the material to adhere to the plate.To ensure plate adhesion, you need to go through several steps because it’s difficult to determine just one culprit: Either the resin isn’t at the correct temperature or it’s fluctuating during the printing process, thus having a negative impact on the resin’s properties. However, sometimes the temperature is the culprit. In this case, a print will adhere well only when the plate is even or finely textured. On the other hand, with bottom-up printers, you might have adhesion problems if the build plate wasn’t adequately prepared. If you’re using a top-down SLA printer, this force is exerted on the model whenever the plate is separated from the vat for repositioning. After a few repositioned layers there will be a higher force pulling away from one side and the printer can’t compensate. Print Plate Adhesion Problemsĭoes your print fail to adhere? Is it floating in the tank or is it partially separated? Adhesion problems occur for several reasons.įirst of all, the printer might be having trouble when positioning the next layer slightly differently on top of the previous layer. So let’s cut straight to the chase and explore the most common reasons why your resin print failed and find the right solution. Resin printing comes with its own set of problems and challenges.
